Why Hager Group has expanded its production in Blieskastel
04 June 2024
Investments - Hager Group has significantly expanded its production of distribution cabinets in Blieskastel. The reason: the fuse boxes have long since evolved into technology centers which are needed everywhere.
In the end, when all the switching elements are screwed in and all cables are laid, Sandra Bayer always asks ‘smart Klaus’. “If I made a mistake, Klaus shows me where,” says the assembly employee. Klaus is a computer that looks like an illuminated workbench.
On it, Bayer places the fully assembled baseplate of a distribution cabinet. The computer scans the part with his camera - and quickly gives the green light: Everything is in its place!
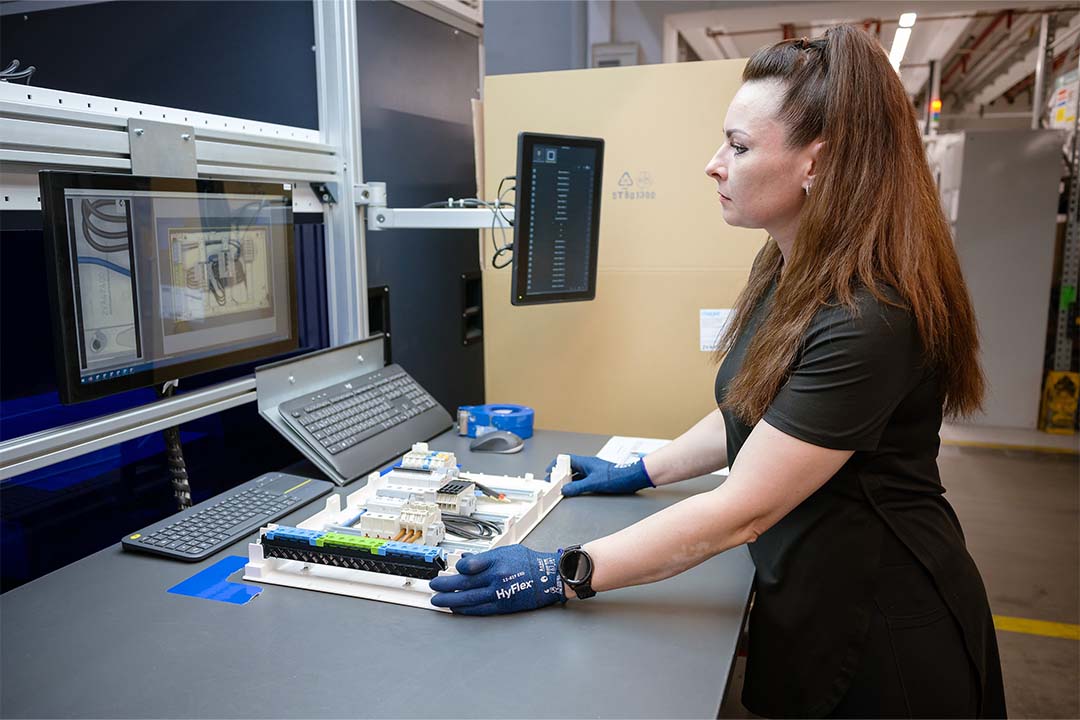
High-tech for testing: Antonia Sitner presents a fully assembled part to "Smart Klaus" – a computer that scans it with a camera.
The company has invested around 40 million euros.
This "smart Klaus" is brand new, just like much else at the Hager electrical technology specialist's plant in Blieskastel. The family-owned company has invested around 40 million euros in its Saarland headquarters. 28 new machines have been acquired. Why such a big investment at this location?
To answer these questions, Stefan Frevel, sales manager for Hager Germany, explains: “Hager is a pioneer in the energy transition in the building sector”.
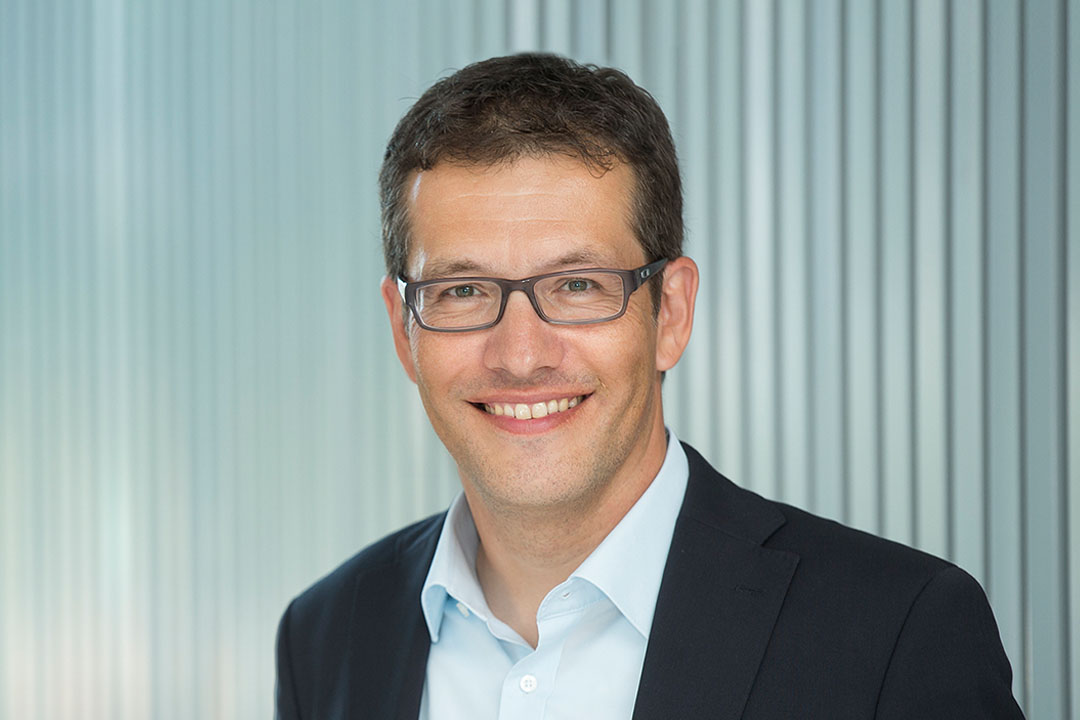
Stefan Frevel, Hager Group Country Sales Senior Director Germany
"Our vision is that we help shape the electrical world of tomorrow." Shaping the world electrically – that's what Hager has been doing since it was founded in 1955. The success formula of the family business is simple: every modern building needs electricity - and it cannot be safely controlled without distribution cabinets, circuit breakers, and other technology. Today, Hager Group is active in over 100 countries and has plants in ten countries, including Germany, France, Poland, Spain, and Italy. However, 40 percent of the company's sales are made in Germany.
Here in Saarland as well as at the plant in Obernai, France, Hager produces its best known product: the distribution cabinet. It comes in various sizes and shapes, whether made of metal (for the German market) or plastic (the preferred variant in France). To understand why Hager specifically expanded the production of these products, one must take a closer look at this large piece of technology – which here is obligatory for all buildings.
"In the past, distributors only needed to count electricity and protect lines," Frevel explains. About 40 years ago, the residual-current circuit breaker was added: it can prevent an electric shock, for example, if a child sticks their hand into a toaster. "But today, distributors have to do much more." The energy transition means an increasing number of buildings now generate their own electricity with solar panels. New major consumers such as wall boxes or heat pumps have been added, as well as fiber optic connections and smart home applications. All these cables (and their software) now come together in the distributor: "The meter cabinet of the past has become a technology center," says Frevel. And this electrical heart of the energy transition will beat in the future not only as standard in new buildings. Existing properties and businesses are also upgrading their buildings piece by piece.
The new machines have not displaced manual labour
The workshops in Blieskastel reflect Hager’s response to this increased demand. Where there used to be wide corridors between the production lines, the 25,000 square meters are today "remarkably tightly packed," as plant manager Ingo Strassburger puts it.
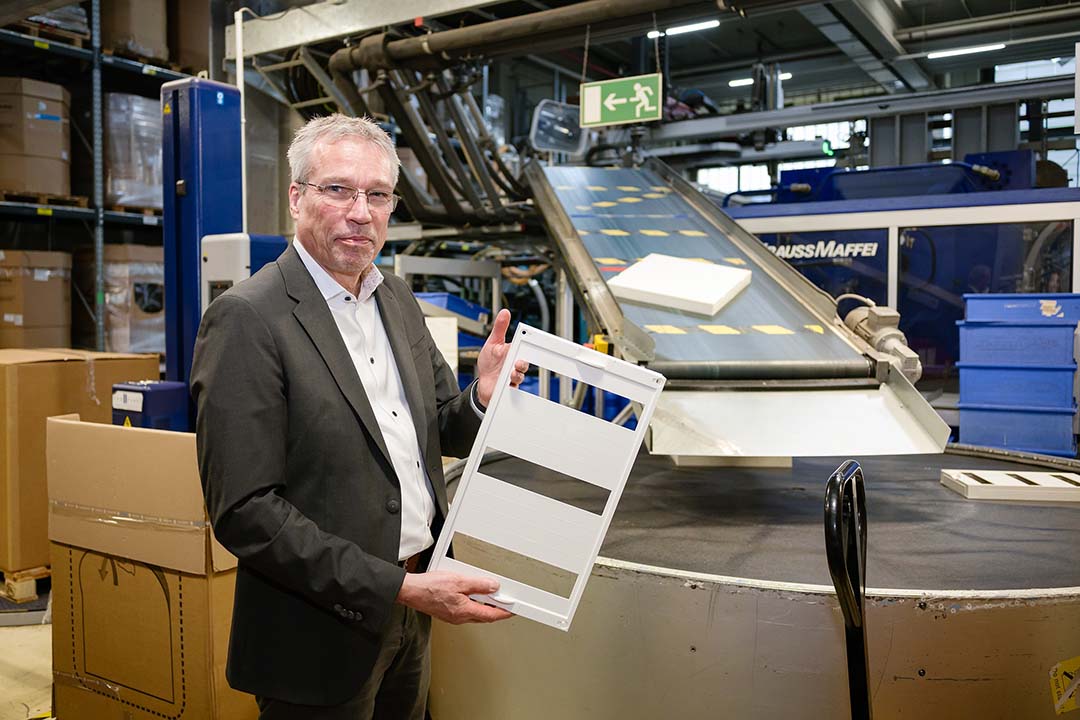
The cover of a distribution panel: "We have an extremely high production depth," explains plant manager Ingo Strassburger.
The new systems – mostly injection molding machines – have been set up not only during ongoing operations but also on the existing space. Human and machine must therefore work closely together. They have decades of experience in this here – as seen in an older machine that takes up almost a quarter of the workshop: At the front, an employee lays sheet metal from a steel coil, and at the back, a finished cabinet housing comes out. In between, the machine cuts, welds, and bends the metal into shape – a "miracle of engineering," says Strassburger.
"We produce around 350,000 cabinets a year, the record is 10,000 per week." Nevertheless, there are still many purely manual workplaces, as the plant manager emphasizes. The interiors of the distributors, for instance, with their cables and switches, are still produced by hand.
All plastic parts for this are manufactured by Hager itself and then assembled by employees like Sandra Bayer. The 43-year-old enjoys her job – also because the products she makes are so useful.
“If I have to explain what I do at Hager, I say: energy distribution cabinets. If your fuses ever blow, you can think of me!”
Switching elements and cables: Sandra Bayer assembles the interior of a distribution cabinet.
Conveyor belt to the painting area: The metal housings are coated with a special white powder coating.
Text: Michael Aust, Wirtschaftszeitung aktiv
Photos: Oliver Dietze
This article appeared on May 13 in German in the Saarland edition of the business newspaper aktiv and at https://www.aktiv-online.de/
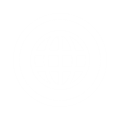