Distribution centre for Albert Heijn
A new distribution centre for Albert Heijn was recently opened on the Beiraweg in Amsterdam, focusing on the home delivery of groceries in the Amsterdam, Haarlem and North Holland regions. The so-called Home Shop Centre (HSC) can process up to 40,000 orders per week. With 20,000 m², the e-fulfilment centre is by far the largest HSC in the supermarket chain.
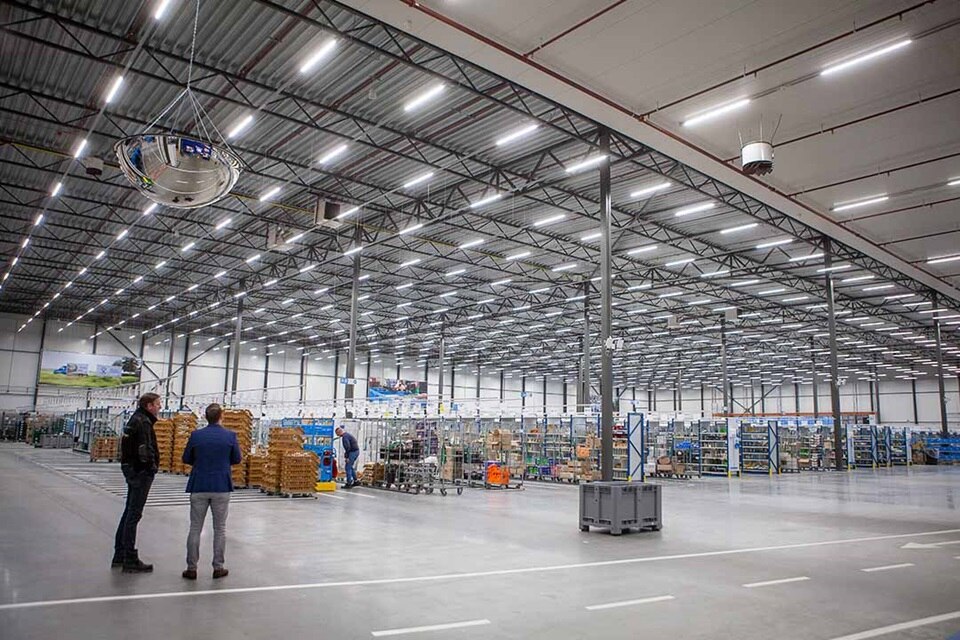
The new distribution centre is located in an existing logistics building, which has been thoroughly rebuilt for this new function. The most important adaptations include the construction of various loading and unloading facilities for trucks and vans and the conversion of a 2,000 m² mezzanine into office space. A new main entrance has also been added. PV panels have been placed on the roof of the distribution centre. In addition, the building-related installations have been replaced. A lot of attention was paid to the power supply because Albert Heijn wants to solely use electric delivery vehicles in the long term. The design for the Home Shop Centre was made by Wubben Chan Architects. De Vries and Verburg signed for the execution, while HoffmanDME Techniek is responsible for the complete electrical installation. From the medium-voltage installation, cable ducts, rail ducts and power connections for cold stores and machines to the LED lighting.
"Nice one-two”
Spread across the distribution centre are five Hager subdistributors, built and supplied by panel builder partner Apko Electric B.V. A Hager main distribution board has also been installed in the meter cupboard space on the ground floor. Due to the high amperage, this main distributor was not ordered from the panel building partner, but directly from the manufacturer. "A nice one-two, because both we and Apko Electric B.V. work regularly with Hager and the Hager products," says Maurice Hoffman, director of HoffmanDME Techniek. "We have an open communication and the short lines of communication means we can switch quickly in every project. The level of knowledge of Hager's account managers and support staff is high, and we are also very pleased with the product quality. Malfunctions and breakdowns of the main and subdistributors are hardly an issue. Our mechanics regularly follow product training courses at Hager, so that they are well aware of (new) techniques and assembly methods. This benefits the quality and speed of our projects".
Joint engineering
"In this project, together with HoffmanDME Techniek, we took care of the engineering of the main distributor," says Chris Louwrier, account manager at Hager. "Based on the HoffmanDME Techniek block diagram, our technical specialist and project manager Daniel Leermann made a preliminary design for the main distributor. This design was discussed with the E-installer and where necessary, optimisations were made, after which we delivered the final design to panel builder partner GTV. After construction, we took care of the transportation to the construction site and the moving in of the main distributor, as well as the connecting it to the distribution boards. Because Albert Heijn wants optimum insight into the consumption of the various groups and in order to keep up the speed of the project, we also wired out, connected and set up various energy meters during the work. We worked closely with the manufacturer of the energy meters, Janitza.
Construction form 2B
A Hager IP40 Weber Unimes system of 3,200 Amps has been installed in the HSC, which is fully certified according to IEC-EN-NEN 61439-1/2. "Where normally 4B is used for larger distributors, 2B was deliberately chosen for this project," says Louwrier. "In the cabinet, the main busbar is separated from the switches, power supplies and other functional components by means of an aluminium plate. By opting for this less complex design, a considerable amount of time was saved. In addition, this solution is very cost-effective".
In order to comply with the IP40 class, Hager mounted the cartridge switch-disconnector-fuses behind the cabinet door for the first time, where they are normally integrated into the front of the distributor. In addition, a 2,000 Amps outgoing field is provided in the distributor. From here, a 135-metre-long rail sleeve goes to the other side of the building, to supply power to the cold stores. "Instead of our own rail sleeve, HoffmanDME Techniek has opted for an EAE rail sleeve system," says Louwrier. "We had very close contact with EAE to ensure that this busbar duct could be properly connected to our main distributor in one go.
Phase 2
The Albert Heijn distribution centre was opened in mid-November 2019. At the moment another car park is being built on the adjoining 12,000 m² site, which is intended to accommodate 500 cars. Hager distribution cabinets will also be installed here, which will be built and supplied by Apko Electric B.V.
"Nice one-two”
Spread across the distribution centre are five Hager subdistributors, built and supplied by panel builder partner Apko Electric B.V. A Hager main distribution board has also been installed in the meter cupboard space on the ground floor. Due to the high amperage, this main distributor was not ordered from the panel building partner, but directly from the manufacturer. "A nice one-two, because both we and Apko Electric B.V. work regularly with Hager and the Hager products," says Maurice Hoffman, director of HoffmanDME Techniek. "We have an open communication and the short lines of communication means we can switch quickly in every project. The level of knowledge of Hager's account managers and support staff is high, and we are also very pleased with the product quality. Malfunctions and breakdowns of the main and subdistributors are hardly an issue. Our mechanics regularly follow product training courses at Hager, so that they are well aware of (new) techniques and assembly methods. This benefits the quality and speed of our projects".
Joint engineering
"In this project, together with HoffmanDME Techniek, we took care of the engineering of the main distributor," says Chris Louwrier, account manager at Hager. "Based on the HoffmanDME Techniek block diagram, our technical specialist and project manager Daniel Leermann made a preliminary design for the main distributor. This design was discussed with the E-installer and where necessary, optimisations were made, after which we delivered the final design to panel builder partner GTV. After construction, we took care of the transportation to the construction site and the moving in of the main distributor, as well as the connecting it to the distribution boards. Because Albert Heijn wants optimum insight into the consumption of the various groups and in order to keep up the speed of the project, we also wired out, connected and set up various energy meters during the work. We worked closely with the manufacturer of the energy meters, Janitza.
Construction form 2B
A Hager IP40 Weber Unimes system of 3,200 Amps has been installed in the HSC, which is fully certified according to IEC-EN-NEN 61439-1/2. "Where normally 4B is used for larger distributors, 2B was deliberately chosen for this project," says Louwrier. "In the cabinet, the main busbar is separated from the switches, power supplies and other functional components by means of an aluminium plate. By opting for this less complex design, a considerable amount of time was saved. In addition, this solution is very cost-effective".
In order to comply with the IP40 class, Hager mounted the cartridge switch-disconnector-fuses behind the cabinet door for the first time, where they are normally integrated into the front of the distributor. In addition, a 2,000 Amps outgoing field is provided in the distributor. From here, a 135-metre-long rail sleeve goes to the other side of the building, to supply power to the cold stores. "Instead of our own rail sleeve, HoffmanDME Techniek has opted for an EAE rail sleeve system," says Louwrier. "We had very close contact with EAE to ensure that this busbar duct could be properly connected to our main distributor in one go.
Phase 2
The Albert Heijn distribution centre was opened in mid-November 2019. At the moment another car park is being built on the adjoining 12,000 m² site, which is intended to accommodate 500 cars. Hager distribution cabinets will also be installed here, which will be built and supplied by Apko Electric B.V.
Project: Distribution centre for Albert Heijn
Location: Amsterdam, Netherlands
Products & Solutions: Hager main distribution board, Hager subdistributors, Hager IP40 Unimes system
www.hager.nl
Location: Amsterdam, Netherlands
Products & Solutions: Hager main distribution board, Hager subdistributors, Hager IP40 Unimes system
www.hager.nl
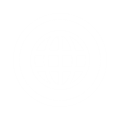